Client
Société Tunisienne des Industries de Raffinage
Location
Zarzouna - Bizerte
Start of work
2014
Delivery date
2014
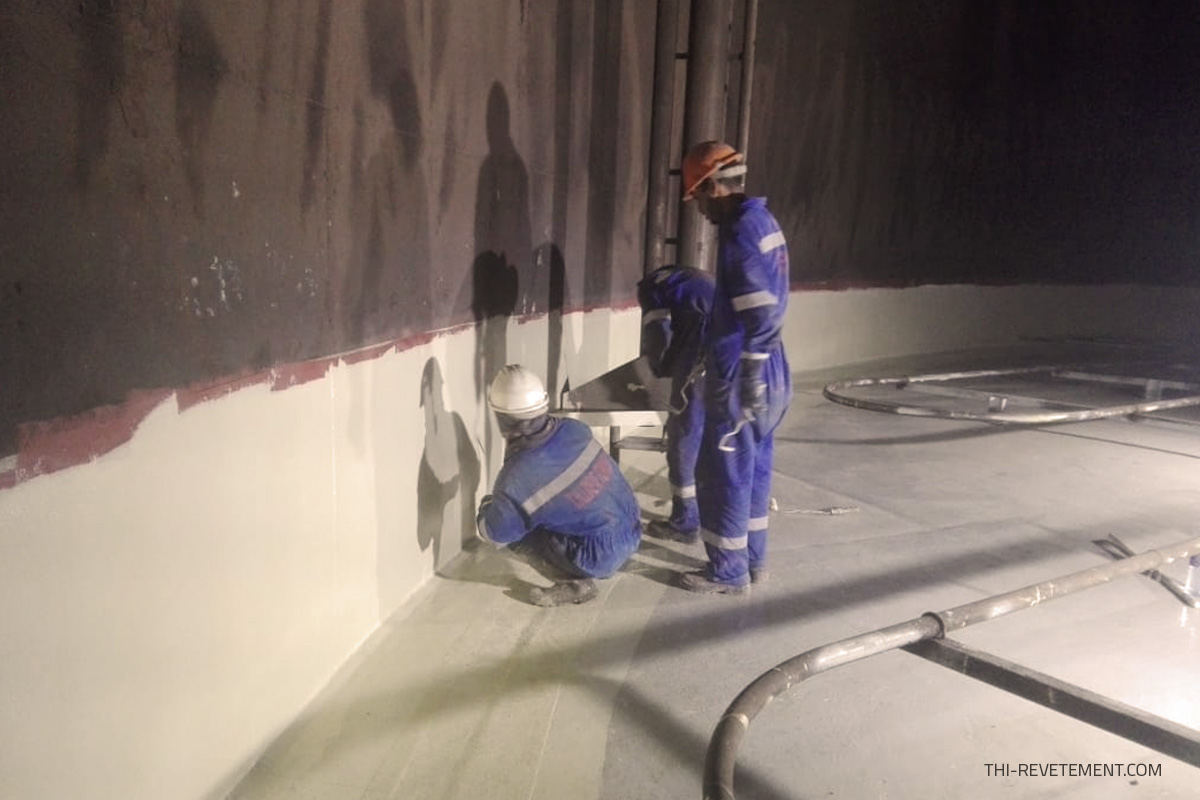
Old hydrocarbon storage tanks are taken out of service periodically to inspect the bottom which is subject to severe corrosion which causes leak holes which cause considerable losses of the stored product and cause the tank to stop operating for long durations.
The purpose of our intervention is to extend, by means of a special anti-corrosion coating, this period of technical inspection of the bottom up to a minimum of 10 years by applying a shot blasting operation followed by a reinforced anti-corrosion coating on the bottom and 1 m of the tank shell to protect it against the stresses of corrosion for a long time.
The intervention of T.H.I REVETEMENT consists first of all in the surface preparation of the bottom by shot blasting; is a surface treatment technique, the purpose of which is to expose the steel, improve the appearance of the surface, increase its roughness and guarantee perfect cleaning of the weld beads and deteriorated surfaces.
Shot blasting is done through the mechanical projection of small steel balls which are projected at high speed and continuously.
The shot blasting operation makes it easy to reach the SA3 level of preparation.
The shot blasting guarantees a high roughness which is essential for a good adhesion of the anti-corrosion coating system on the surface of the bottom.
As soon as the shot blasting is finished, a waiting coat of epoxy anti-corrosion paint is applied, which serves to protect the bare surface after the shot blasting.
The anti-corrosion coating system is composed of layers of an epoxy resin without carcinogenic mutagenic substances or dangerous for reproduction, so as not to affect human health.
The internal anti-corrosion coating system is reinforced with fiberglass matt to improve the mechanical resistance of the anti-corrosion coating system.
The anti-corrosion coating system is then closed with a layer of reinforced resin which improves the sealing of the system.
The anticorrosion coating system will be checked at the end by an electric field to test the existence of air bubbles or the weakness of thickness.