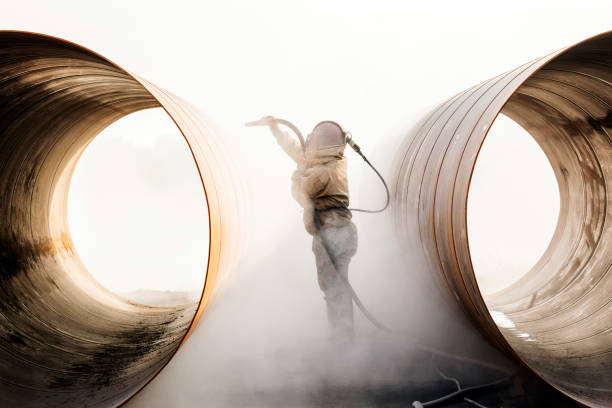
Sandblasting is an industrial technique for cleaning large surfaces using an abrasive sprayed at high speed with compressed air through a nozzle onto the surface to be pickled
brasive blasting is a manual technique that allows a surface to be mechanically treated with a sandblasting machine for the purpose of pickling it or simply cleaning it to bring it back as close as possible to its original state. The use of a professional sandblaster is usually recommended for the pickling of metal surfaces, such as steel, aluminum, stainless steel, …
Sandblasting or Abrasive blasting is based on the principle of pneumatic spraying of abrasive at high speed onto a support to be treated. The choice of the abrasive is made according to the support and the expected result also according to whether the purpose is a pickling, a treatment before coating or a finish. There are two main principles of sandblasting: Vacuum and pressure brasive blasting.
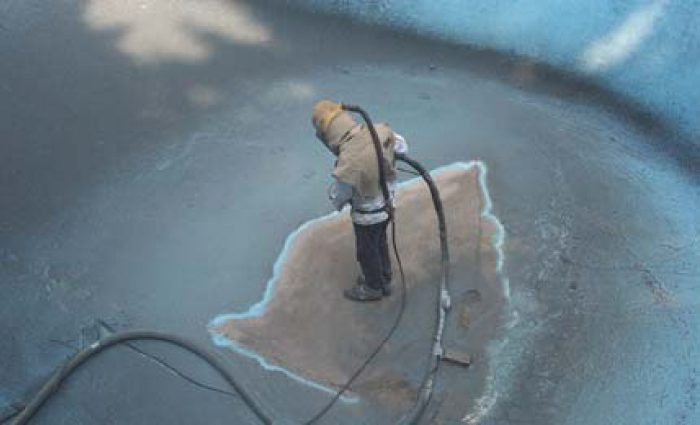
Vacuum Sandblasting involves the use of compressed air in a gun to create a vacuum that will suck the abrasive before it is ejected. Pressure sandblasting involves pressurizing a tank containing abrasive to pneumatically transport the abrasive through a piping system to be sprayed at high speed through a nozzle.
The vacuum or pressure Sandblasting machine is a pneumatic equipment that requires compressed air for its operation. Depending on the principle chosen and the diameters of the ejection tips, the required air flow rate will vary. The sandblasting context can sometimes be dangerous and many standards govern its practice both in terms of equipment and in terms of the operator’s protective equipment.
In some cases, the use of the hydrogumming technique allows, by adding water to the abrasive blast, to significantly reduce the spark emissions and dust emissions generated by the abrasive and the support. Sandblasting can also be used in the building sector for cleaning facades, urban furniture, statues, floors … on supports such as stone, granite, bricks, cement, concrete, bronze, wrought iron, ….
More and more, on these softer materials (where we also find wood, marble, tuffeau, glass, plastic), the technique of aerobgumming is increasingly used as a substitute for brasive blasting.
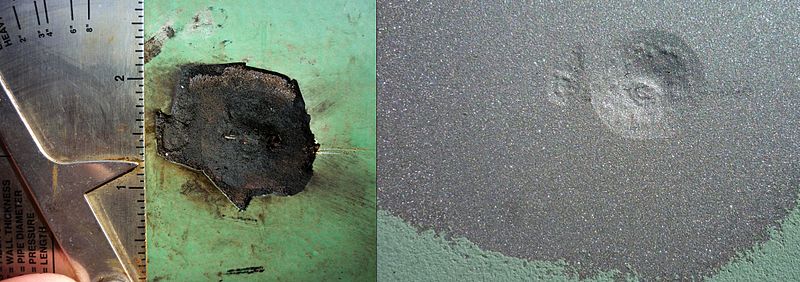