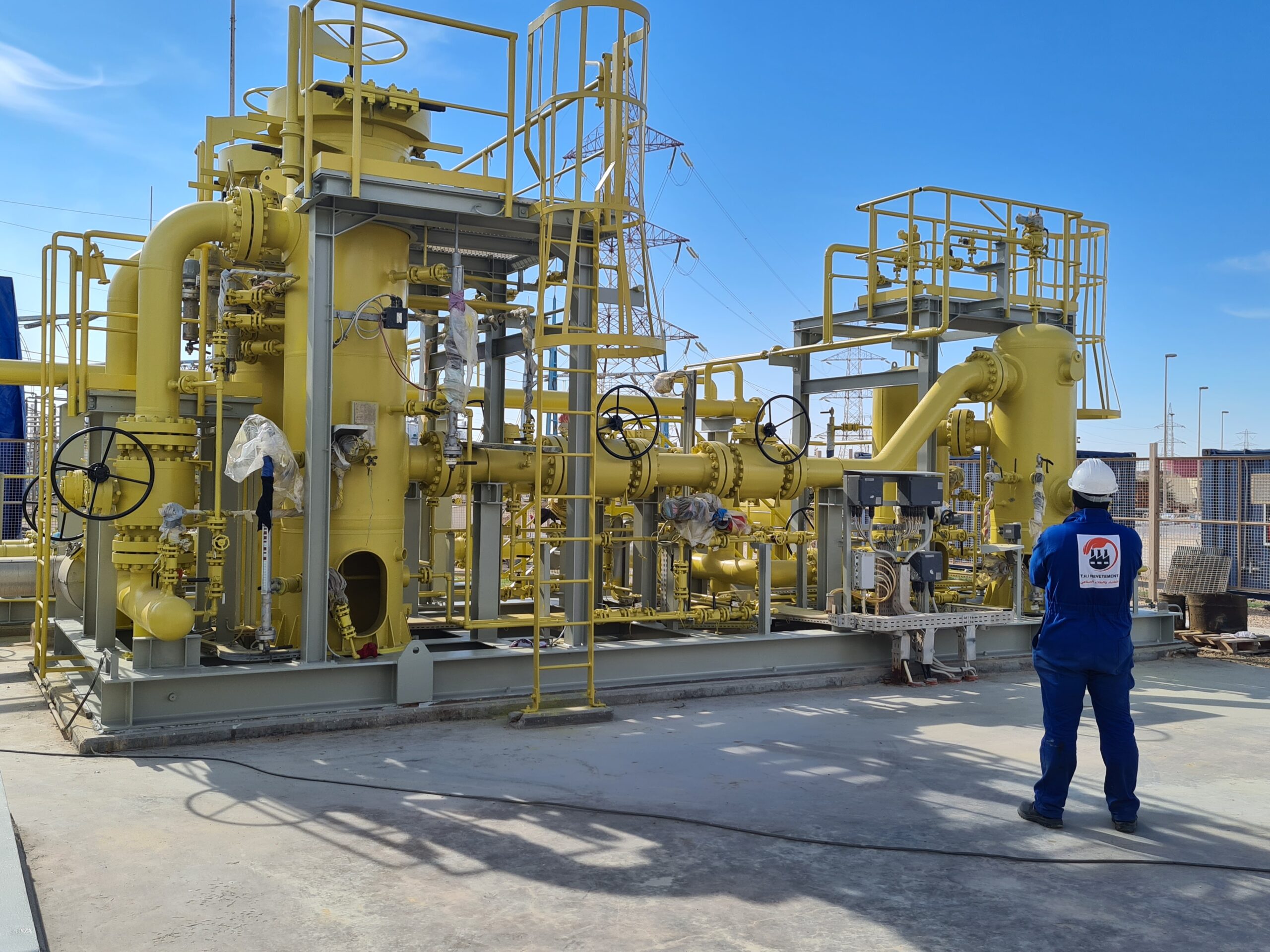
1- What is corrosion :
Corrosion is defined as any chemical reaction that leads to the deterioration of the material.
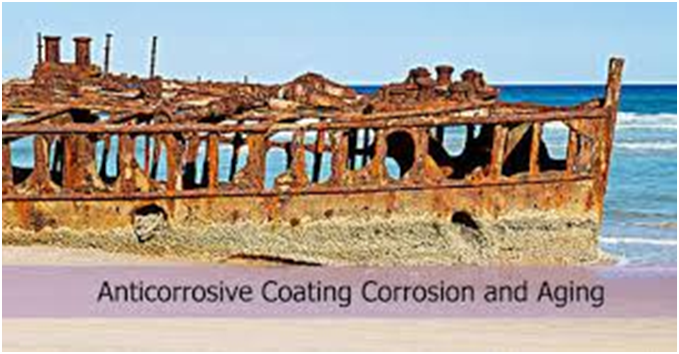
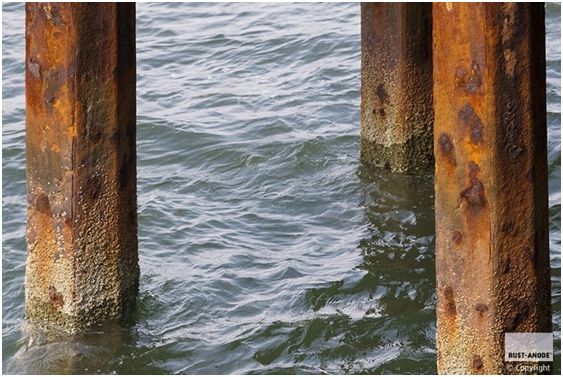
2- Protecting a surface with an anti-corrosion coating
A corrosion protection or anti-corrosion coating is an association on the surface of one or more layers of a material that is considered lazy to react chemically with the material that is causing the corrosion.
The type of anti-corrosion coating is defined according to the material of the surface to be coated (steel, cast iron, concrete, …) and the material that causes the corrosion (water, air, acid, salinity, …).
The purpose of the anti-corrosion coating varies according to the case, it can be for :
– Protection of the steel against corrosion deterioration
– The extension of the life of the coating support
– Strengthening of metal and steel structures
– Protection of stored products against contamination
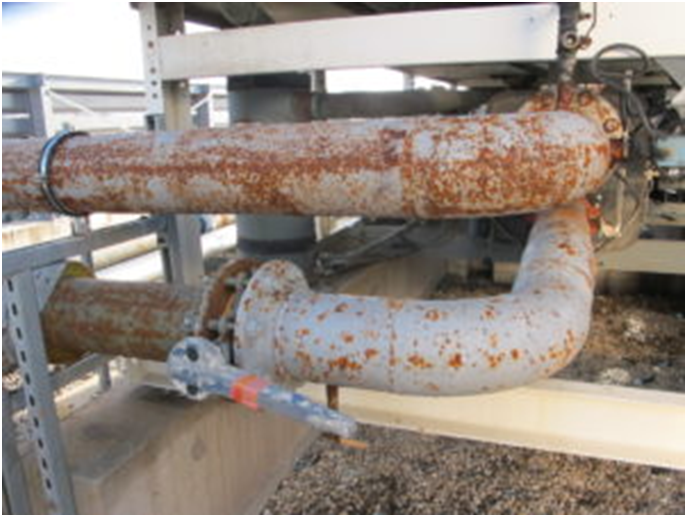
3- Anti-corrosion coating for steel substrates
An anticorrosion coating is normally intended to protect materials sensitive to oxidation, especially steel and aluminum.
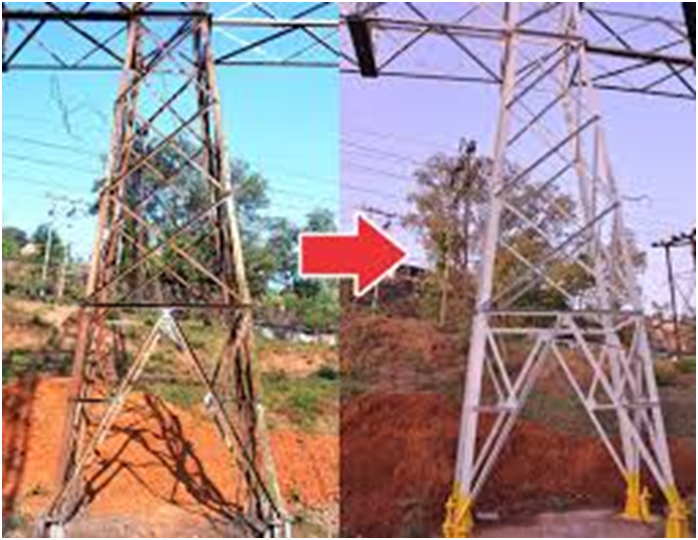
3-1- Physical form
The techniques for applying coatings to these materials depend on the material of the anticorrosion coating itself and its physical state:
-Liquid (paint, resin,…)
– Powder (paint)
– Solid (rubber, brick, PVC,…)
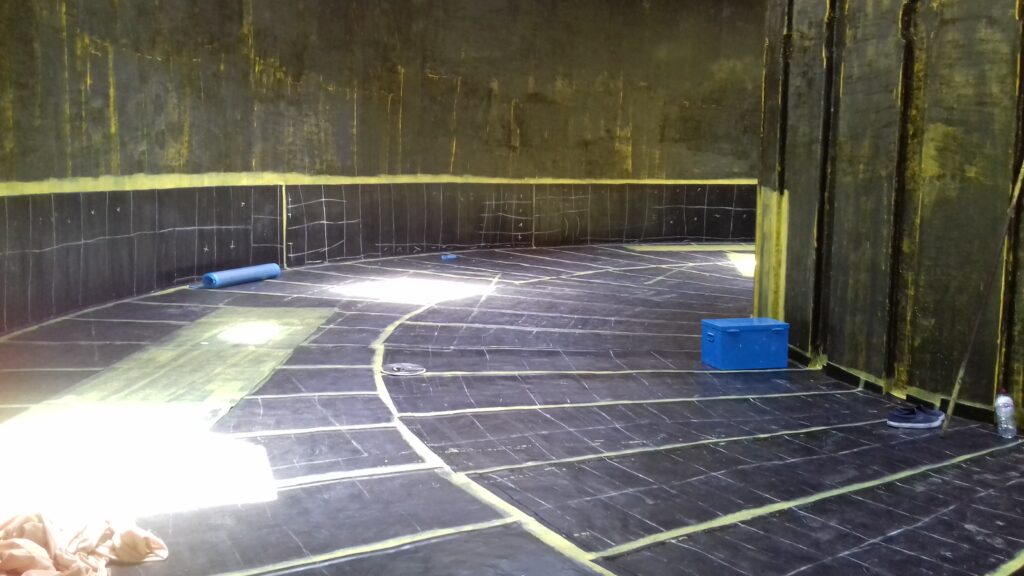
3-2- Influence of the place
Also a technique of application of anti-corrosion coating can vary for the same support depending on the site where it has undergone this coating, example for galvanized surfaces that are coated by dipping in the workshops but by applying a cold galvanization in the installation.
4- Techniques of application of an anticorrosion coating:
4-1 Surface preparation :
The application of an anticorrosion coating must be preceded by a surface preparation (stripping).
The purpose of the surface preparation is to clean the surface and increase the roughness for a good adhesion of the coating.
A surface preparation (stripping) can be done by :
– Mechanical stripping (sandblasting, shot blasting, brushing, …)
– Hydraulic stripping (high pressure water)
– Chemical stripping
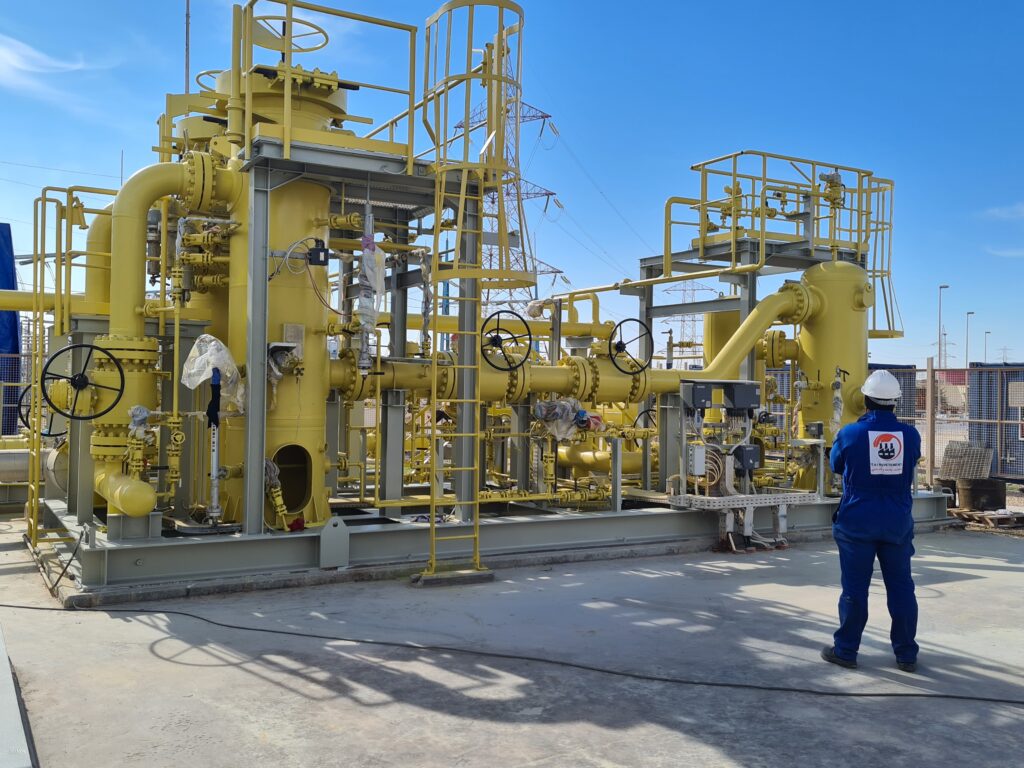
4-2- Application of an anticorrosion coating
Each anti-corrosion coating is applied according to its condition and viscosity, for example
– Pneumatic spraying (paint)
– Airless pumping (paint, resin)
– Manual application by brush or roller (resin)
– Application by gluing with suitable glue (sheet coating such as rubber)
– Laying by cement resin (solid coating such as brick)
– Fixing by screw (PVC plate)
– Other methods
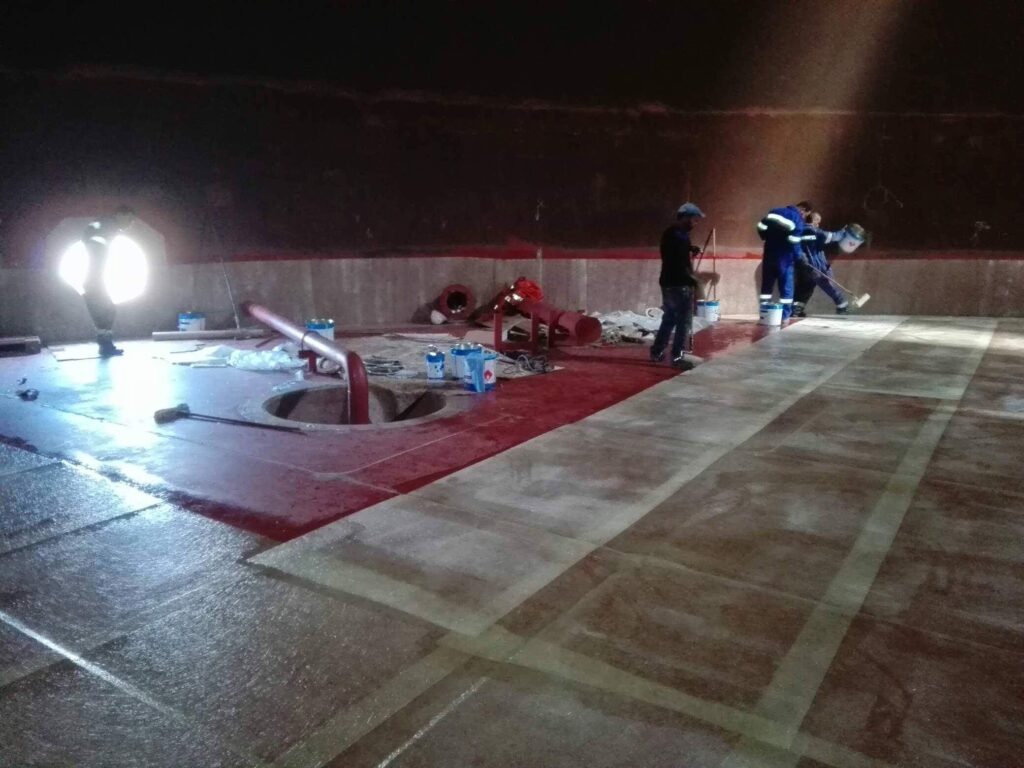
5-General :
The use of anti-corrosion coatings is very important in the world and the market is expanding successively.
The most important consumer is the amount of steel used in the construction of industrial and civil facilities worldwide.
Older industrial, marine and civil structures, as well as bridges and pavements, are also potential consumers of anti-corrosion coating products.
The manufacturing companies are generally each specialized by a coating product depending on the field of application and the type of corrosion stress and the nature of the coating material.
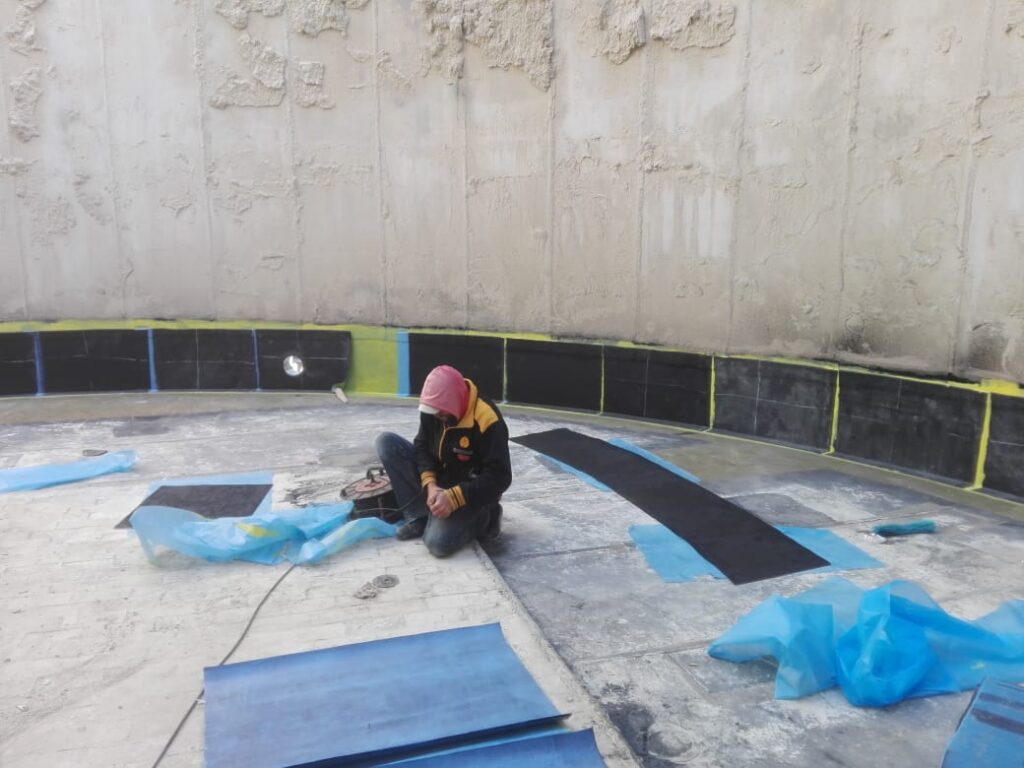
Application companies are specialized by the application site and the type of coating, e.g. galvanizing is done in workshops, electrostatic painting is done in workshops, while repair and maintenance coatings are done directly on the installations.
Some of our projects;
- Micro concrete projection, butyle rubber coating and anti-acid carbon brick coating of the phosphoric acid reactor R3601A – GCT
- Welding, sandblasting and anti corrosion coatings of the port portal of the silo of Cereals Office
- Paving works and coating of the Skhira sulphuric cell with acid-resistant plate GCT
- Dielectric coating on the floors of the electrical room of unit 1000 of the phosphoric acid plant Gabés – GCT
- Anti-clogging coating of the walls of the hopper and the phosphate storage silo at the Skhira plant TIFERT
- Repair of the boilermaking and ebonite coating of the equipment of the concentration loops A ,B,C & D Skhira – GCT