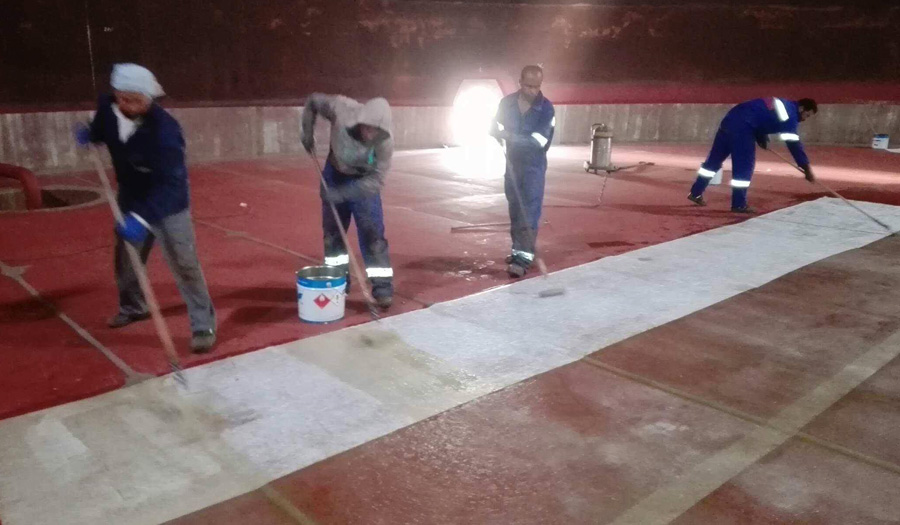
Crude oil storage – tank bottom rehabilitation
What Does Tank Lining Mean?
Anti-Corrosion lining or Anti-Corrosion coating designed to cure at low temperatures and is applied inside and outside a tank to provide the ultimate protection of the substrate material from chemical attack.
The Anti-Corrosion Lining offers corrosion resistance and maintains toughness in metallic, plastic and concrete tanks, which offers storage for petroleum products, chemicals and other reactive solvents.
In storage crude oil often contains salt water and sediment that settles out at the bottom of the tank. Chlorides and other soluble salts contained in the water may provide a strong electrolyte that can promote corrosion.
Generally, corrosion due to immersion exposure creates a surface that is rough and pitted, which is difficult to completely coat with a thin-film lining system.
Our Services: – Corrosion Control – High-voltage line towers – Maintenance of Storage tanks – Industrial Plastic Pipes – Maintenance of high-voltage electrical transformers – Micro-concrete and shotcrete |
Crude oil storage – tank bottom rehabilitation – pitting in steel
There are generally two common types of corrosion pit:
Generally caused by electrochemical (Cathode) corrosion. Simple enough to fill in using special mastic to ensure complete coverage.
Generally caused by ‘microbial induced corrosion’ (MIC).
Sulfate-reducing bacteria (SRB) found in the layer of sludge at the bottom of crude oil storage tanks creates an aggressive cycle of corrosion which creates the distinctive ‘omega’ shaped pit.
It can be difficult to coat the entire surface of the pit with traditional application techniques and should be opened up by grinding or repaired using welding.
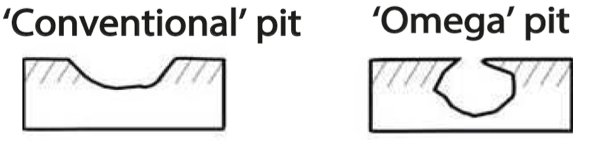
Crude oil storage – tank bottom rehabilitation – Fiber reinforcement
Thick film, high solids lining systems offer better coverage and edge retention when applied to pitted substrates, extending the life of the coating system.
A glass fiber matt reinforcement is essential to achieve a waterproof system that provides high capacity and improves system life.
The thickness of the Anti-Corrosion Lining to be applied depends on the state of the tank bottom, level of loss of thickness caused by corrosion, the age of the bottom, …
Generally for a new bottom applies a lining of 2 mm thick and 3 mm thick for an old bottom .
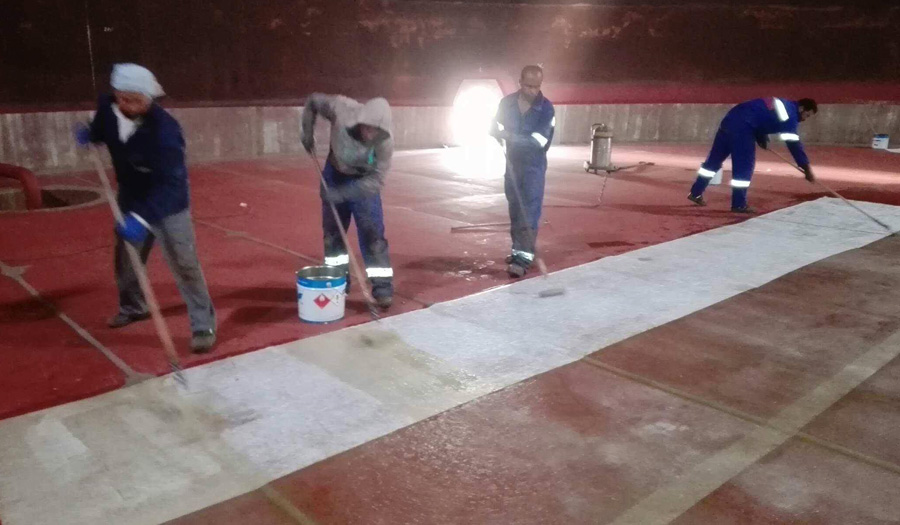
Cost & Comparison
The price of hydrocarbon tank linings (Anti-Corrosion Lining) depends directly on its diameter, , but the commercial cost depends also on other parameters such as the volume of work, the workplace, the type of tank roof (floating or fixed), the degree of corrosion on the bottom.
Generally the cost’s Anti-Corrosion Lining varies between 6% and 10% of the fuel’s value stored in the tank. In case of leakage, in addition to the stored fuel that will be lost, additional losses will be required such as work to recover the stored product, work to clean up oil waste, work to treat polluted areas, shortfall because of the tank stand by and the penalties imposed by the environmental protection authorities, so the lining’s cost varies between 3% and 5% of the total cost of losses.